Plansee reference
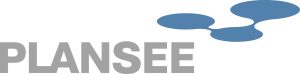
pitFM – our leading facility management system
> 4.200
Helpdesk messages per year
> 90
Different helpdesk functions for 3 company divisions
130
Suppliers
> 2.400
Work orders per year
Plansee SE
As a high-tech company with production and sales companies around the world, Plansee supplies customers from many future-oriented industries with high-tech metal products. The focus is on the production and processing of the metals molybdenum and tungsten.
Initial situation and objectives
In 2008, Plansee decided to implement the pitFM software. The aim was to improve infrastructural building management in order to optimally map and manage service tenders in the area of cleaning. In addition, a smooth helpdesk process was to be ensured. Thanks to the optimized documentation options, it is now possible to record technical data and connection documentation (switchgear, transformer, etc.) as well as failures and influences on technical equipment. Using the SAP interface, information such as master data on cost centers and hazardous materials is transferred to pitFM on a daily basis and processed further. All CAD plans for the Reutte property are integrated into the system and are constantly being expanded. In the meantime, the emergency lighting equipment, fire alarms and workplace staff assignments have also been referenced between AutoCAD and pitFM.
Since summer 2013, all laws and regulations have also been mapped with pit Legal Compliance. Helpdesk processing in the Technical Service FM area has been extensively updated and various key figures have been taken into account for e-mail dispatch. Processing takes place in the interaction between pitFM Smart and pitFM Mobile. The accident reporting system will be expanded online in 2020 to include fire, explosion and environmental protection. The new workplace evaluation module went live in 2020 and is constantly being expanded and supplemented to meet current requirements such as the integration of hazardous substances (SAP data sheets), federal and state specifications (integration of current links) and extensive catalogs (hazards/risks and measures). The circle closes when conditions are documented on site during planned or spontaneous inspections and evaluations with the help of the mobile device and are initiated and delegated in a standardized manner in the form of helpdesks for prompt processing.
Customer
Plansee SE
Industry
Industry, metal production
Head office
Reutte, Austria
pit products & solutions in use
Supported processes
Service management
Maintenance management
Space management
Waste management
Fault message management
Fire protection book
including mobile inspection
Key management
Cleaning management
SAP interface
Data management
Data migration from Aperture
Document management
Work and hazardous substance management
Fleet management
Booking management